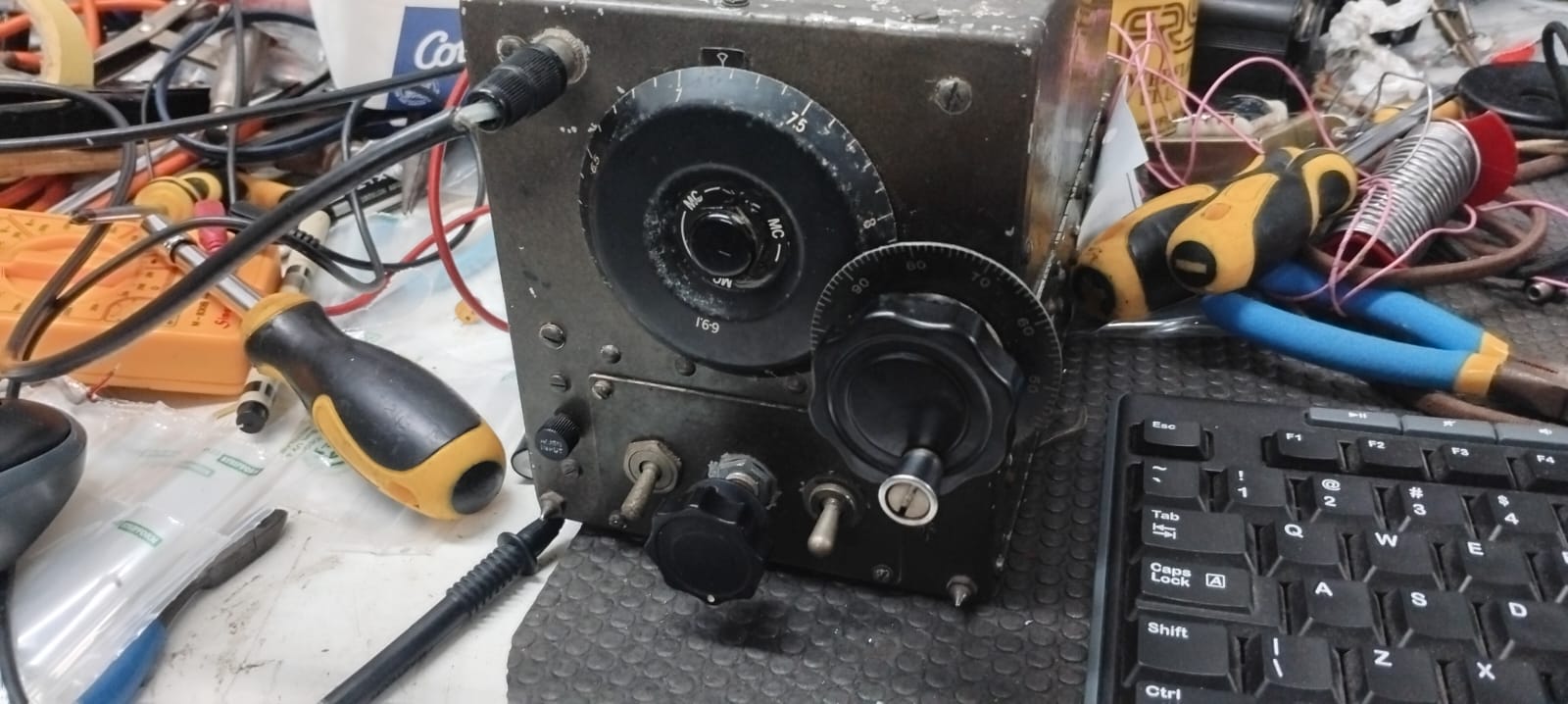
A little update
This is the first actual blog post to the website. The others were older articles that i wrote up to a year ago.
Article:
I got this receiver a while back from a guy up north. I got this BC455, its accompanying transmitter, and a modulator unit for the transmitter. Those other two will be covered in a future post. They are all part of the SCR274 command set (also known as the ARC5 command set)
When I received the radio it was in pretty decent condition compared to the other parts of the SCR274 set I have so far.
I also got hold of dynamotor for the receiver (not the original type but still the correct voltage) from John ZS1WJ. That worked when i received it. I tested all the valves in the BC455 with my vintage valve tester and they all tested good. The BC455 had been re-wired to 12V on the filaments instead of 24V, which suited my dynamotor just fine since it also required 12V instead of 24V.
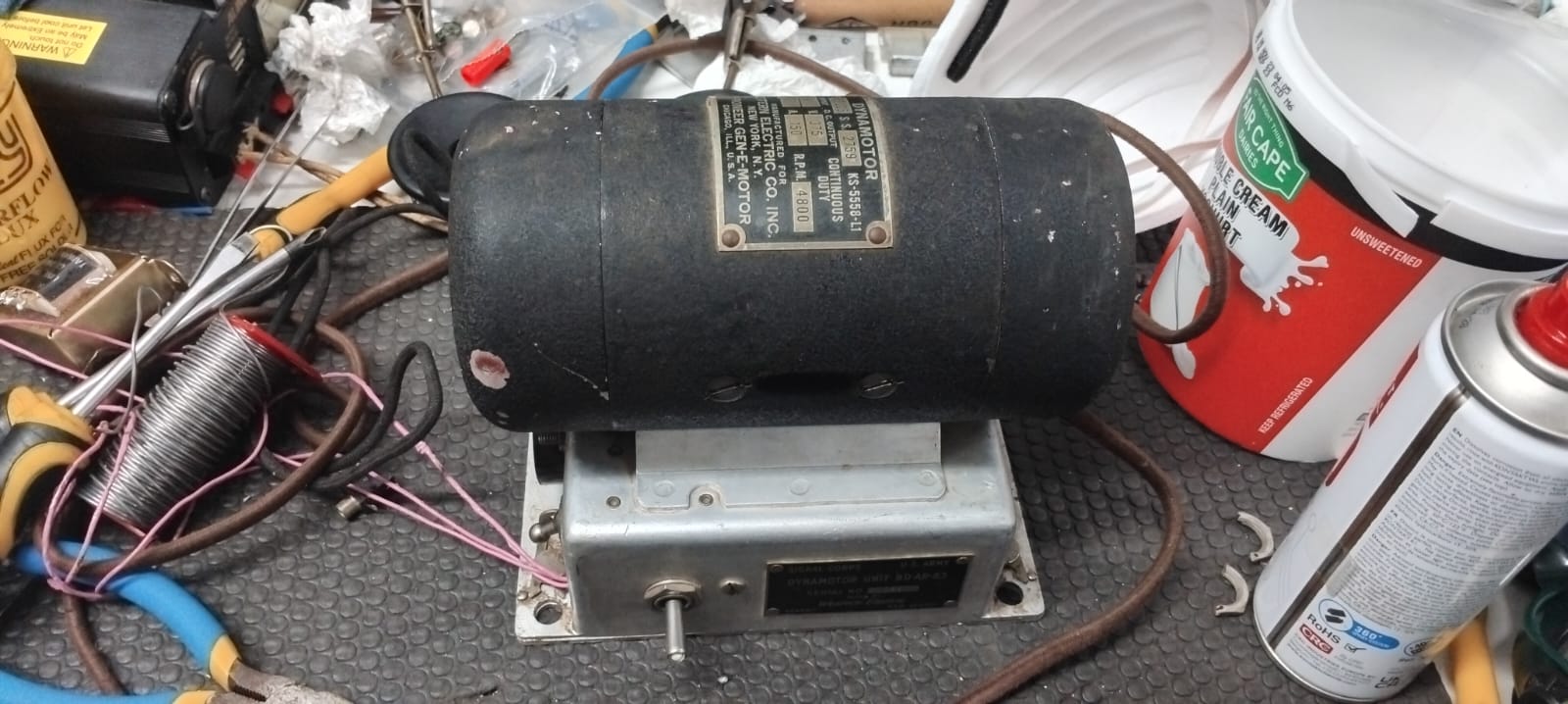
I wired up the BC455 to the dynamotor and gave it power from my 13.8V 30A psu (13.8V is close enough to 12V that it works fine). Turns out that the dynamotor chassis is connected to +375V and the “HV out” is actually the ground of the dynamotor. This means that I gave the BC455 -375V which caused the smoothing capacitor inside to let the magic smoke out.
A pool of “liquid” came out of the capacitor and went on the mat that i was working on. Later I found out that this was the highly toxic PCB oil (Polychlorinated Biphenyl oil). I wiped it up, clipped the lead that went to the capacitor so that I wouldn’t effect the operation of the rig. I then corrected the wiring of the rig so that there was +375V on the HV in on the receiver and the ground was actually grounded. I gave it power and hooked up a speaker to it and heard some noise.
I then used my TinySA spectrum analyzer to generate a signal and feed it into the antenna input of the receiver. I tuned the signal in with the help of a oscilloscope on the audio output since the audio was extremely soft. It worked perfectly. I ended up replacing the audio transformer with a different one that gave much less distortion and more volume.
There was one more issue: there was no way to add a knob to the since it was designed to be remote controlled via a wire that physically attached to the gearbox. I removed all the valves, the IF boxes and the gearbox to get to the back of the connector (both the valves and the if boxed are socket-ed which is great). I had to cut the connector bit off since it was screwed on and then two pins were put in so that it couldn’t unscrew. After I had done that I just added a knob and all worked well.
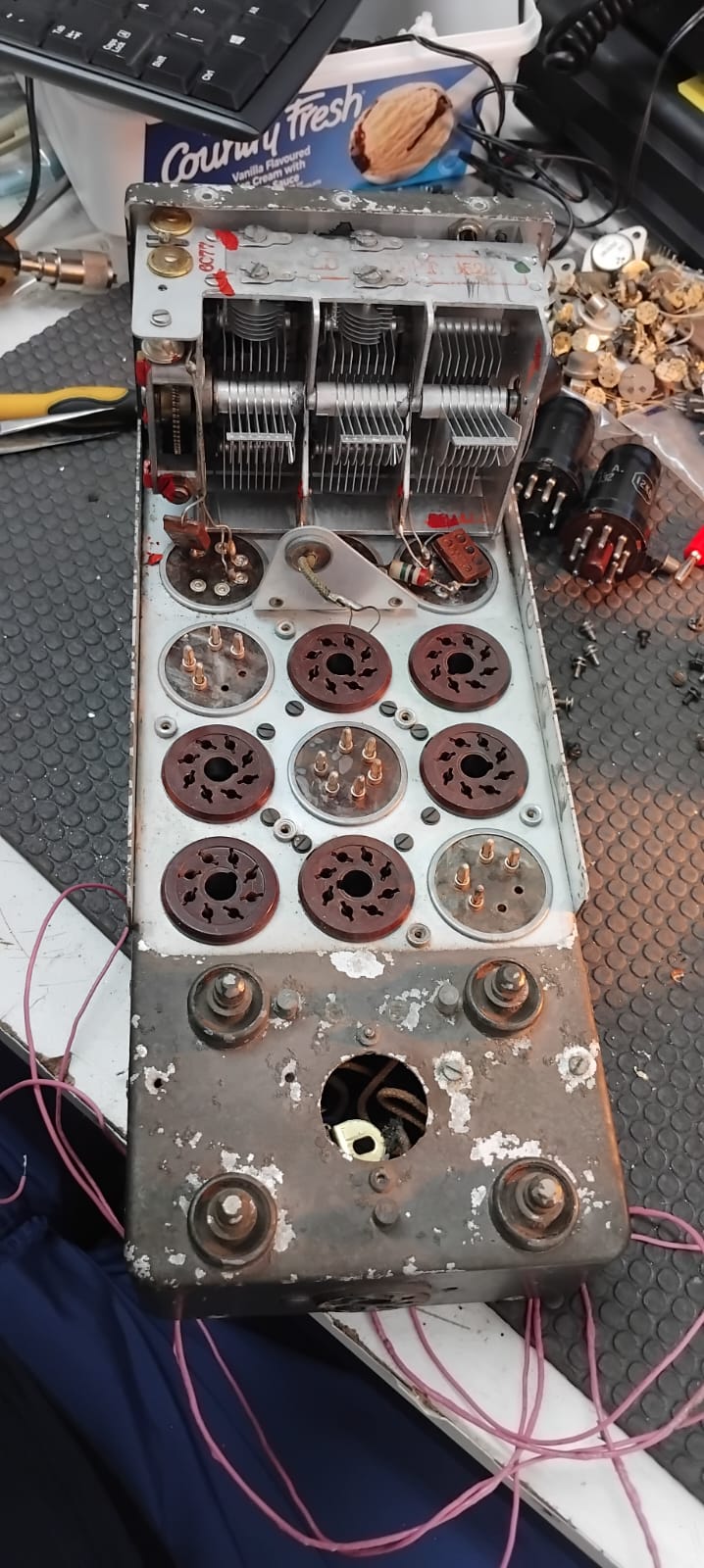